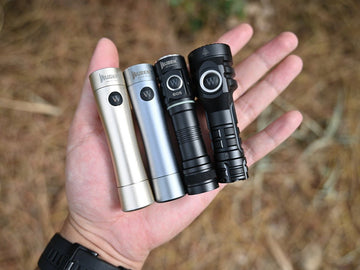
Materials used in flashlights
Flashlights are available in a variety of materials. Here, we will describe common materials used and terminology related to material properties so you can choose the flashlight to best suit your needs.
Enjoy a 15% discount on all Wuben X series products, including X0, X1, X2, and X3.
Aluminum alloy
For most high-quality flashlights, the most common material used for the body is aluminum alloy. This is because of its strength, ability to transmit heat and conduct electricity, all whilst having a low density.
Aerospace-grade aluminum alloy
Some flashlights are made from 'aerospace-grade aluminum'. This group includes 2024-(T3 or T351), 7050-(T7451 or T6) and 7075-(T6/T651 or T7351). 7075-T6 is the most common. These alloys are anodisable but cannot be welded.
Aircraft-grade aluminum alloy
6061-T6 is the most common type of 'aircraft-grade' aluminum alloy. It is used in flashlights because of its hardness and high tensile strength.
What is anodizing?
Anodising is done to make an aluminum alloy surface more resistant to wear and corrosion. It also makes the surface more suitable for painting. Anodising is when the aluminum alloy surface is oxidized.
Type III anodizing is called hard anodising. It provides a coat of aluminum oxide which is less porous, more deeply embedded and thicker than Type II anodizing.
How is anodizing is done?
The aluminium alloy is placed in a bath of sulphuric acid. Oxygen forms around aluminium alloy. This becomes a coat of hard aluminium oxide on the surface.
The aluminium alloy is the positive electrode (anode) when it is placed in the sulphuric acid bath.
The aluminium alloy becomes thicker after anodising. It also becomes more resistant to chipping and peeling. Type III anodised flashlights are available in more colours.
Anodising prevents the aluminium alloy from being conductive, so some areas of the torch will deliberately not be anodised, such as the end of a tube or on threads, to allow conductive metal-to-metal contact.
Other flashlight materials
Titanium alloy
Titanium is more resistant to corrosion than stainless steel and is 40% less dense.
It is more denser than aluminium alloy, but much stronger. This makes it more difficult to machine and more expensive. It also does not conduct heat as well as aluminium alloy.
Higher-end custom flashlights are made from titanium alloy. This material can be polished to become very shiny. It can also be bead blasted and anodised for a variety of colours.
Stainless steel
Stainless steel is steel that has 11% or higher chromium content. It does not transmit heat from an LED as well as aluminum. It can have a variety of surface treatments such as high gloss of matte and is sometimes magnetic, but not always. Stainless steel is much heavier than aluminum alloy, but much harder.
Copper
Copper is denser than aluminum alloy and titanium. Copper has excellent thermal conductivity. Over time the surface develops a patina (tarnishes) from oxidation, but it can be polished to shine. Copper flashlights have smooth feeling threads.
Brass
Brass is an alloy of copper and zinc. Like copper, brass also develops a patina, but to a lesser extent. It can also be polished. It is golden in color and slightly less dense than copper and not as good as transferring heat than copper or aluminum alloy.
Terminology used when describing material properties
Material hardness
'Hardness' is a scientific term for a material's ability to withstand permanent deformation. Deformation can be due to cutting, abrasion, penetration and scratching. Indentation hardness is a common way in which material hardness is measured. One scale used to measure hardness is called the Rockwell Scale.
Scratch hardness is measured using the Mohs Scale where various materials can be compared. Talc has a value of 1 and diamond has a value of 10.
The most commonly used test to determine hardness is the Brinell scale. The test is carried out by applying a load to the surface of the material using a hardened ball. HB is the units for Brinell hardness.
Density
Density is defined as the mass per unit volume and is measured in g/cm^3 of kg/m^3. If a material is denser, it is heavier for the same volume than a material with lower density.
Tensile strength
This is the amount of pulling or stretching that a material can withstand without being permanently damaged. If the yield point is passed, the damage cannot be reversed. Ultimate tensile strength is a material's maximum resistance to fracture.
Thermal conductivity
This is the material's ability to conduct heat. Thermal conductivity units are Watts per metre-kelvin [W/(m K)] in the SI system.
Table of material properties
The table below will help you to compare material flashlights and can help you in choosing your most suited one. Higher density material flashlights will feel heavier. Ones with higher hardness and ultimate tensile strength will have more resistance to wear and those with higher thermal conductivity will have better cooling properties, which is an important property for high output flashlights.
Material | Density [kg/m^3] |
Hardness/Brinell scale [HB] |
Ultimate Tensile strength [Mpa] |
Thermal conductivity [W/(m K)] |
Aluminium alloy 2024-T3 | 2780 | 120 | 483 | 121 |
Aluminium alloy 6061-T6 | 2700 | 95 | 310 | 151 |
Stainless steel | 7982 | 149 | 505 | 25 |
Copper | 8944 | 89 | 210 | 401 |
Titanium | 4520 | 379 | 1170 | 17 |
Brass | 8587 | 60 | 338 | 111 |
Plastic polymer
Finally, we will look at plastic polymer as a material for flashlights. Plastic is often regarded as material used in flashlights for its lower cost and lower density, however, there are some settings where it is essential to have a flashlight made from this.
Heat conductivity is generally an advantage in flashlights, but sometimes it is not desirable, especially in situations where users work in extremely high heat environments, such as fire fighting. In fire fighting, tools used for rescue are not made from any kind of metal and a metal flashlight can cause burns if exposed to heat.
Plastic polymer flashlights are ideal in environments with dangerously high temperatures, because they conduct heat at a much slower rate, so will not get as hot as quickly. They will be safer to handle and better at protecting the batteries in extremely hot environments.
In some professional environments, such as areas where explosive gas mixtures are present, aluminum flashlights will not conform to safety standards and will not be allowed.
Metal flashlights are also better electrical conductors but this can be a disadvantage as they will be potentially hazardous for electricians who can often work around loose electrical wires. Metal flashlights can create electrical shorts which can damage property or even worse, cause an electric shock to a person. Plastic polymer flashlights are excellent insulators, so will be much safer for electricians to use at work.
Certain additives are added to the plastic resins to make the plastic flashlights compliant with safety standards, which include graphite fibers or organic chemical compounds. These are added so the flashlight dissipates electrostatic charge build-up from friction (such as rubbing it on clothing) so will not spark due to a static electricity build-up.
Excellent article